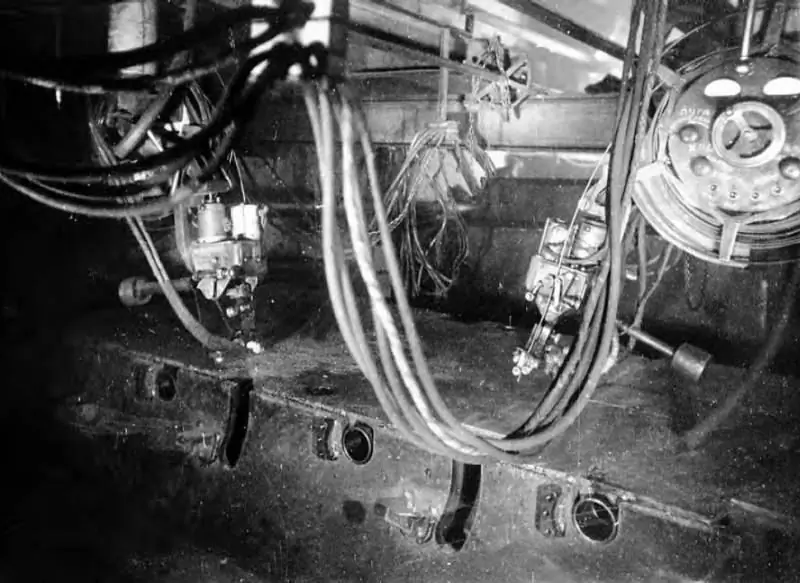
اهلی کردن زره
یکی از مشکلات اصلی در تولید بدنه و برجکهای مخازن متوسط T-34 ، ترک خوردگی در قطعات جوش داده شده بود. همه چیز در مورد سختی بالای زره 8C است ، هنگامی که پارگی یا ریز ترک های کوچکی در کنار درز جوش داده شده ایجاد می شود. وجود تنش های باقیمانده پس از جوشکاری در اولین بار پس از تولید خودروی زرهی خود را محسوس نکرد ، اما با گذشت زمان با ترک هایی به طول 500 میلی متر ظاهر شد. همه اینها البته مقاومت در برابر ضربه زره تانک را کاهش داد. برای حل این مشکل ، بلافاصله پس از سازماندهی تولید شرکت های تخلیه شده ، در نیمه دوم سال 1942 ، متخصصان موسسه زره پوش (TsNII-48) و موسسه جوشکاری الکتریکی آکادمی علوم اتحاد جماهیر شوروی جذب شدند. این تحقیق در دو شرکت انجام شد: کارخانه مخزن اورال شماره 183 در نیژنی تاگیل و کارخانه مهندسی سنگین اورال در سوردلوفسک. در مجموع ، از ماه جولای تا اکتبر ، متالورژیست ها و دانشمندان مواد در مورد تشکیل ترک در هنگام جوشکاری حدود 9500 قطعه زرهی تحقیق کردند. هدف از این مطالعه یافتن بهینه ترین ترکیب شیمیایی زره 8C بود. مشخص شد که مهمترین جزء زره در این وضعیت کربن است. اگر محتوای آن در زره بیش از 0.25 بود ، سختی منطقه سخت شده در ناحیه درز جوش داده شده به شدت افزایش می یابد ، که به ناچار منجر به ترک می شود.
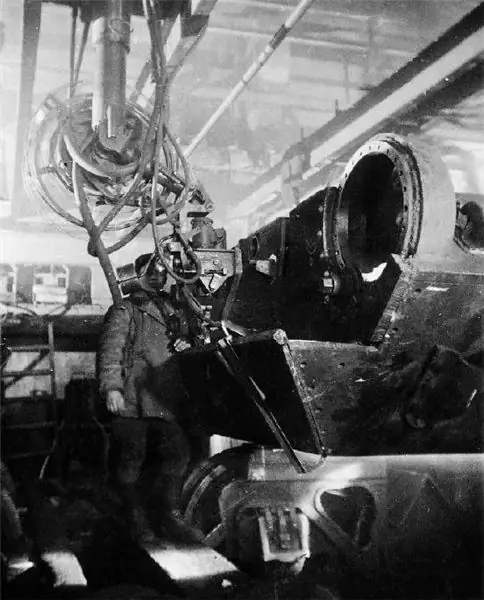
اما اطمینان از میزان کربن کم در فولاد زرهی در زمان صلح آسان نبود و در زمان جنگ به هیچ وجه غیرممکن به نظر نمی رسید. تغییرات کوچک "آرایشی" در چرخه جوشکاری از طریق استفاده از الکترودهای آستنیتی ، یک سیستم چند رول برای اعمال درزهای جوش ، و خنک شدن کم مجموعه ها پس از جوشکاری امکان افزایش حد بالای کربن را تا 0.28 possible فراهم کرد. به به هر حال ، در صنعت تانک آلمان آنها حتی در مورد چنین الزامات جدی برای زره تانک نشنیدند - به طور متوسط ، سهم کربن در محدوده 0.4-0.5 was بود. راه حل مشکل ظاهر شدن ترک ها در ناحیه جوشکاری ، پیش گرم کردن قطعات تا دمای 150-200 درجه سانتیگراد و به دنبال آن خنک شدن آهسته قطعات پس از جوشکاری تا 100 درجه به مدت 30 دقیقه بود. برای این منظور ، موسسه زره پوش سلف های خاصی را ایجاد کرد که گرمایش محلی قطعات زرهی را در منطقه برش یا جوشکاری گاز فراهم می کند. در کارخانه ماشین سازی سنگین اورال ، از سلف ها برای جوش دادن اتصال قسمت جلویی با کناره ها و سقف و همچنین هنگام برش سوراخ های متعادل کننده در قسمت های جانبی سخت شده مخازن استفاده شد. بنابراین ، مشکل ترک خوردن در حین جوشکاری فولادهای زرهی با کربن متوسط حل شد. با گذشت زمان ، کارخانه Sverdlovsk به سایر کارخانه های مخزن گسترش یافت.
دستگاه های جوشکاری
در ژوئیه 1941 ، به دستور شورای کمیسارهای خلق ، موسسه جوشکاری الکتریکی آکادمی علوم اتحاد جماهیر شوروی به نیژنی تاگیل تخلیه شد. به همین دلیل است که برای اولین بار جوشکاری قوس الکتریکی زیر بدنه مخزن در اورالواگونزاوود معرفی شد. البته ، این فناوری قبلاً شناخته شده بود ، اما گروه آکادمیک یوگنی اسکاروویچ پاتون با کارکنان TsNII-48 توانستند آن را برای جوشکاری فولادهای زرهی تطبیق دهند. ولادیمیر ایوانوویچ دیاتلوف یکی از دانشمندان برجسته ای که در توسعه جوشکاری زرهی مشارکت داشت.وی به همراه کارکنان کارخانه کمینترن خارکف ، مشکل ترک خوردن زره در حین جوشکاری را با وارد کردن سیم کم کربن به استخر جوش حل کرد (در ادامه مطلب در زیر). در سال 1942 ، یک دانشمند ، اولین در جهان ، پدیده خود تنظیم فرآیندهای قوس الکتریکی را با یک الکترود مصرفی کشف کرد ، که این امر باعث شد تا بتوان طراحی مکانیسم های تغذیه ماشین های جوش را به میزان قابل توجهی ساده کرد. همچنین ، به همین دلیل ، امکان ایجاد سرهای جوشکاری تک موتور نسبتاً ساده ، قابل اطمینان تر و ارزان تر وجود داشت. بدون دیاتلوف ، ایجاد جریانهای م effectiveثر بر اساس سرباره کوره های ذغالی کوره بلند کارخانه متالورژی Ashinskiy ، که "شار سرباره SHA" نامیده می شد ، امکان پذیر نبود. از اکتبر 1943 ، دانشمند ریاست آزمایشگاه جوشکاری اورالواگونزاوود را بر عهده داشت و تا سال 1944 در این موقعیت ماند ، تا زمانی که به موسسه تحقیقاتی مرکزی فن آوری های کشتی سازی منتقل شد.
اما بازگشت به افسانه ای T-34 ، که هرگز به چنین تانک عظیمی تبدیل نمی شد ، اگر نه جوشکاری خودکار بدنه زرهی (برج) آن در کارخانه های شماره 183 و UZTM. استفاده از دستگاههای جوشکاری اتوماتیک باعث شد زمان جوشکاری 3-6.5 برابر کاهش یابد. در همان زمان ، حداقل 40 متر خطوط درز جوش برای هر سپاه مخزن استفاده شد.
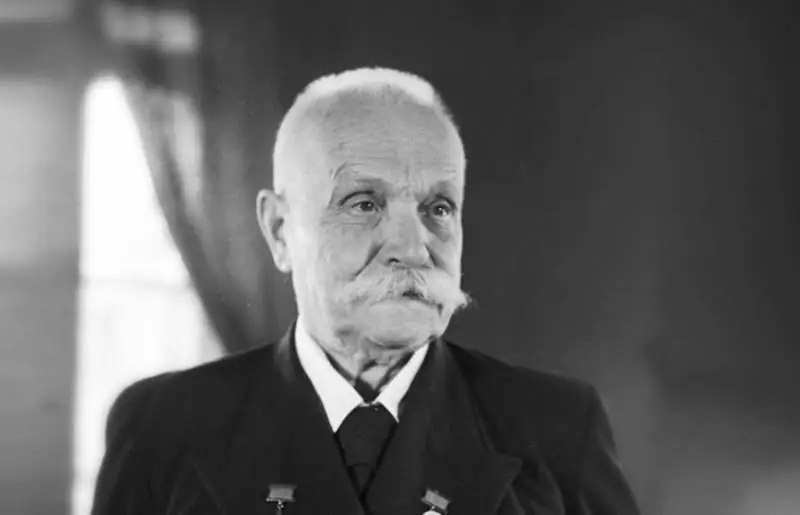
علاوه بر T-34 ، جوش آکادمیک پاتون در کارخانه بدنه زرهی شماره 200 چلیابینسک مورد استفاده قرار گرفت. با کمک آن ، کف بدنه مخزن KV پخته شد ، که در مجموع به ازای هر وسیله نقلیه حدود 15 متر درز بود. مهم است که اتوماسیون جوشکاری زره باعث جذب کارگران کم مهارت به تولید شد - جوشکاران اصلی در طول جنگ با کمبود مزمن روبرو بودند. از ژوئیه 1942 ، یک نوار نقاله مخزن منحصر به فرد در نیژنی تاگیل کار می کند ، که 19 واحد جوشکاری خودکار با قوس غوطه ور در آن کار می کردند. مقیاس نوآوری را برآورد کنید-این امر 280 جوشکار با کیفیت بالا را برای کارهای دیگر آزاد کرد و 57 کارگر کم مهارت را جایگزین آنها کرد. آکادمیسین یوگنی اسکاروویچ پاتون خود در یادداشتی خطاب به دبیر بخش صنعت مخازن کمیته منطقه ای Sverdlovsk حزب کمونیست اتحادیه بلشویک در مارس 1942 در مورد اثربخشی معرفی جوشکاری اتوماتیک (نقل قول N. Melnikov کتاب "صنعت مخازن اتحاد جماهیر شوروی در جنگ بزرگ میهنی"):
"با توجه به بهره وری بالا از جوشکاری اتوماتیک با سرعت بالا در زیر لایه های شار ، زمان جوشکاری بدنه ها به میزان قابل توجهی کاهش می یابد و مصرف نیروی کار ، برق و سیم الکترود کاهش می یابد."
مقایسه زمان صرف شده برای جوشکاری دستی و خودکار را می توان در بایگانی مجتمع نمایشگاهی OAO NPK Uralvagonzavod یافت. به گفته آنها ، برای جوشکاری ، جوشکاری تقریباً پنج ساعت طول می کشد ، به عنوان مثال ، بخشی از بند شانه برجک T-34 ، و جوشکاری خودکار می تواند این کار را فقط در 40 دقیقه انجام دهد. اتصالات پایین به صورت دستی در سه ساعت و در حالت اتوماتیک - در یک ساعت جوش داده می شوند.
برای درز مبارزه کنید
نمی توان گفت که دستگاههای جوش اتوماتیک به طور ناگهانی در کارخانه های مونتاژ صنعت مخازن شوروی ظاهر شدند. اولاً ، سهم جوشکاری دستی هنوز در تولید محصولات زرهی بسیار زیاد بود ، و ثانیاً ، در ابتدا ، همه چیز با خود فناوری یکنواخت نبود. نمی توان سطح لازم شکل پذیری را به جوش داد - پس از سرد شدن ، سخت و شکننده شد. البته این بیشترین تأثیر منفی را بر مقاومت پرتابه زره داشت. پس از تجزیه و تحلیل دلایل ، مشخص شد که همه چیز در مورد فراتر رفتن از عمق نفوذ فلز جوش داده شده ، مخلوط کردن فلز سیم با فلز پایه و آلیاژ قابل توجه فلز جوش است. گروههای TsNII-48 تحت رهبری I. F. Sribny و موسسه جوشکاری ، به سرپرستی V. I. Dyatlov ، روشهای زیر را برای جوشکاری زره "سرکش" 8C و 2P پیشنهاد و آزمایش کردند. اول از همه ، این جوشکاری چند گذر است ، هنگامی که دستگاه قطعات جوش داده شده را در چند مرحله متصل می کند.این امر نفوذ کم در مفاصل و تشکیل یک درز قوی و انعطاف پذیر را تضمین می کند. واضح است که چنین تکنیکی در شرایط جنگ موثرترین نیست: به هر حال ، جوشکاری چند گذر در مقایسه با یک گذر زمان زیادی را می طلبد.
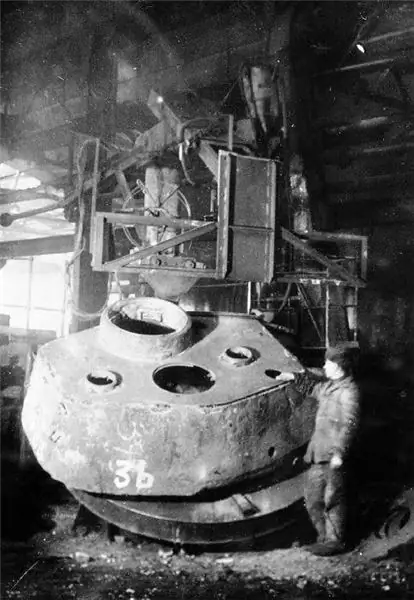
روش دوم از TsNII-48 و م Instituteسسه جوشکاری ، قرار دادن سیم فولادی کم کربن در شیار درزها بود تا "محو شدن" فلز زره را کاهش دهد. در نتیجه ، درز پس از خنک شدن پلاستیکی تر شد ، سیم دمای داخل شیار درز را به طور جدی کاهش داد و همچنین بهره وری ماشین های جوشکاری را دو برابر کرد. این م effectiveثرترین تکنیک بود که حتی بیشتر بهبود یافت. یک روش جدید جوشکاری "در دو سیم" ، که در آن سیم دوم (پرکننده) ، که به منبع فعلی متصل نشده بود ، در استخر جوش با زاویه ای نسبت به سیم الکترود تغذیه می شد. تغذیه و قطر سیم دوم به گونه ای محاسبه شد که مقدار فلز رسوب شده از آن برابر مقدار فلز سیم الکترود رسوب شده است ، یعنی قطر سیم دوم باید برابر قطر الکترود باشد سیم و نرخ تغذیه آنها باید یکسان باشد. اما به دلیل نیاز به تجهیز مجدد سرهای اتوماتیک از تغذیه یک سیم تا تغذیه دو سیم ، معرفی این روش به تعویق افتاد و با روش قرار دادن میله جایگزین آن شد. با این وجود ، در ژوئن-ژوئیه 1942 ، این روش در کارخانه شماره 183 هنگام جوشکاری دسته ای از صفحات پایین بینی بدنه مخزن با تیرهای کمان استفاده شد.
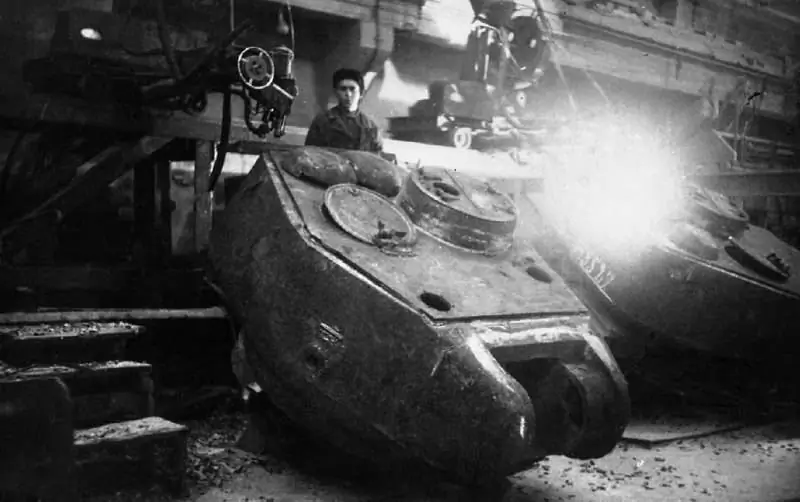
مشکلات مربوط به اتوماسیون جوشکاری مخازن (برجکها) نیز سازمانی بود. شایان ذکر است که دستگاه های جوشکاری هرگز قبلاً به صورت سری مونتاژ نشده بودند و در واقع محصولات تولید آزمایشی موسسه جوش بودند. این توضیح می دهد برخی از کندی در توسعه فن آوری های جدید در صنعت مخازن. بنابراین ، در پایان سال 1942 ، کارخانه های مخزن فقط 30 تا 35 دستگاه جوش داشتند ، که البته کافی نبود. بنابراین ، کمیسر خلق IM Zaltsman ، با دستور شماره 200s 28 مارس 1943 ، در کارخانه شماره 183 دستور داد تا 7 واحد جوشکاری خودکار را تا اواسط ماه مه ، در کارخانه ماشین آلات سنگین اورال تا 1 ژوئن 8 ، اضافی نصب کند. ماشین آلات اتوماتیک و تا 15 ژوئن ، 5 واحد خواستار تحویل به کارخانه چلیابینسک شدند. شماره 200. این مرحله یکی از مواردی بود که به صنعت تانک های داخلی اجازه داد به اهداف تولید برنامه ریزی شده برای خودروهای زرهی ردیابی بسیار مورد نیاز در جلو برسند.