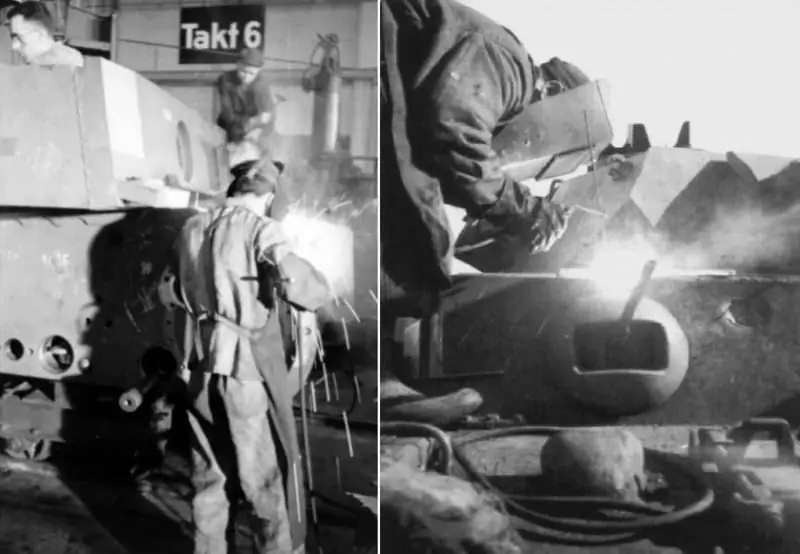
رویکرد آلمانی
در قسمت اول مطالب مربوط به فن آوری های جوشکاری در طول جنگ بزرگ میهنی ، ذکر شد که یکی از اصلی ترین دستاوردهای تکنسین ها و دانشمندان شوروی ، معرفی خودکار جوشکاری بدنه و برج های مخزن بود. در آلمان نازی ، جوشکاری اتوماتیک در کارخانه های مخزن استفاده نمی شد. یک توضیح بسیار مهم برای این امر وجود داشت - در طول دوره اصلی جنگ ، صنعت تانک های رایش سوم با کمبود نیروی متخصص ، از جمله جوشکار مواجه نشدند. و در اتحاد جماهیر شوروی ، هنگام تخلیه شرکتهای بزرگ به شرق ، پرسنل با ارزش برای صنعت از دست رفت ، که نه تنها کیفیت مونتاژ مخزن ، بلکه حتی امکان تولید را نیز به خطر انداخت. در آلمان ، کار به جایی رسید که هنگام جوشکاری بدنه "پلنگ" و "ببر" ، جوشکارهای جداگانه به درزهای جداگانه اختصاص داده شد! مهندس V. V. Ardentov در مورد "تجربه آلمان در برش زره و جوشکاری بدنه تانک" در "بولتن صنعت تانک" در سال پیروز 1945 می نویسد. کار او بر اساس مطالعه دو کارخانه بدنه زرهی در Kirchmeser و Brandenburg بود. بدیهی است که این کارخانه ها تا ماههای آخر جنگ می توانستند چنین لوکس تکنولوژیکی را در قالب جوشکارهای جداگانه برای درزهای جداگانه خریداری کنند.
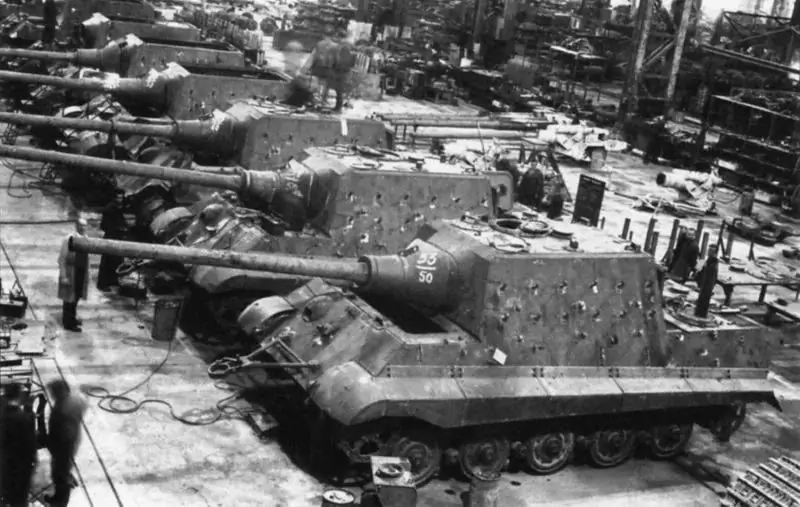
قبل از جوشکاری بدنه ، صفحات زره بریده شد ، که تا سال 1942 به صورت مکانیکی انجام شد. برای برش صفحات زرهی برای اتصالات خار به خار ، استفاده از برش استیلن-اکسیژن بسیار راحت تر بود ، که در شرایط مشابه در صنعت مخازن شوروی نیز استفاده می شد. در اینجا آلمانی ها از نظر کارایی و کیفیت برش از تانک سازان ما جلوتر بودند. این تا حد زیادی نتیجه استفاده از ابزارهای با کیفیت بالا (ماشین های برش گاز مسر و گریشهایم) با قابلیت تنظیم دقیق ضخامت صفحه زره است. همچنین ، آلمانی ها از اکسیژن با درجه تصفیه بالا - بیش از 99 used استفاده کردند. سرانجام ، در هنگام برش زره ، آلمانی ها از چندین مشعل ، از جمله برای پخ زدن استفاده کردند. فرآیند برش شعله به خودی خود انجام شد - این امر باعث شد که این فرآیند تسریع شود و بسیار دقیق تر شود.
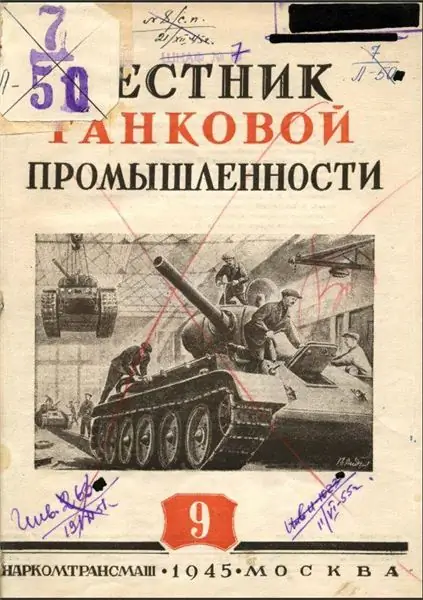
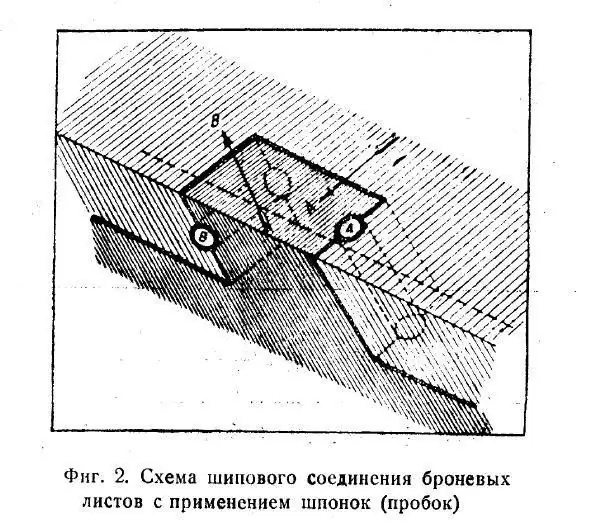
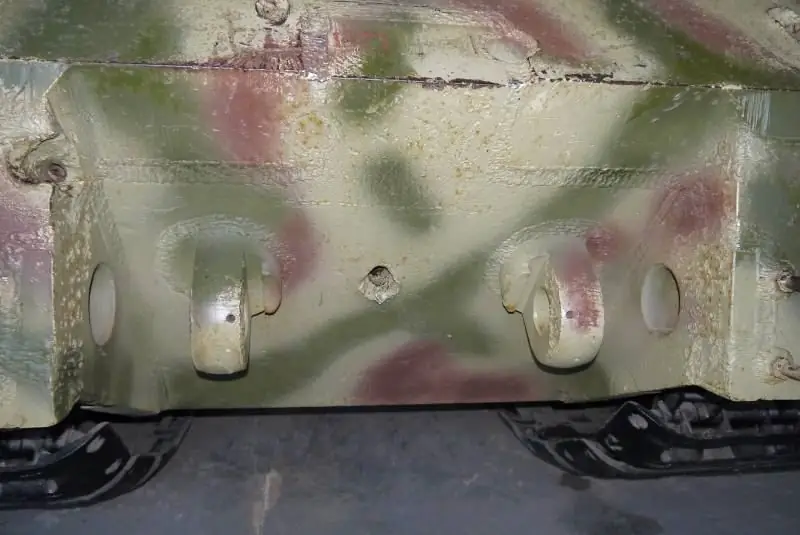
[مرکز]
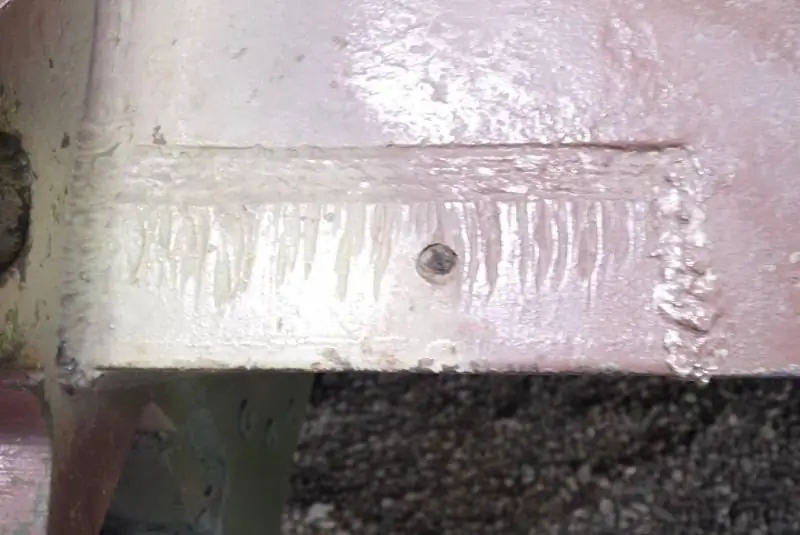
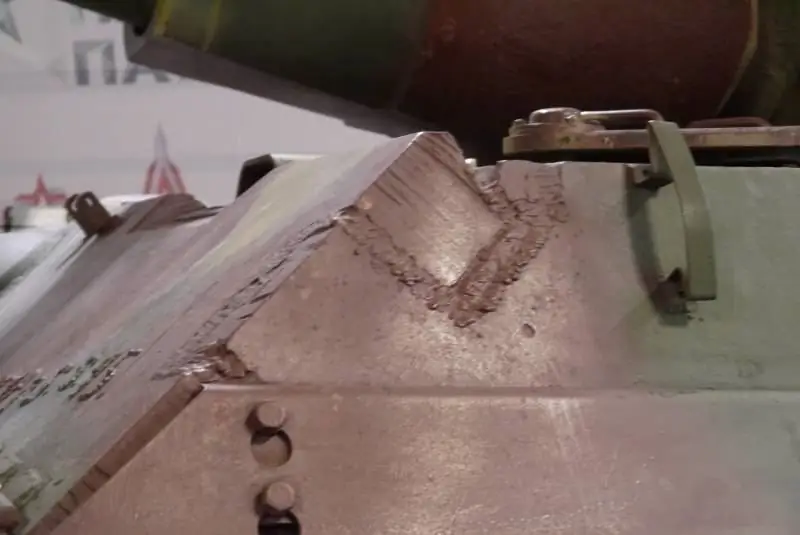
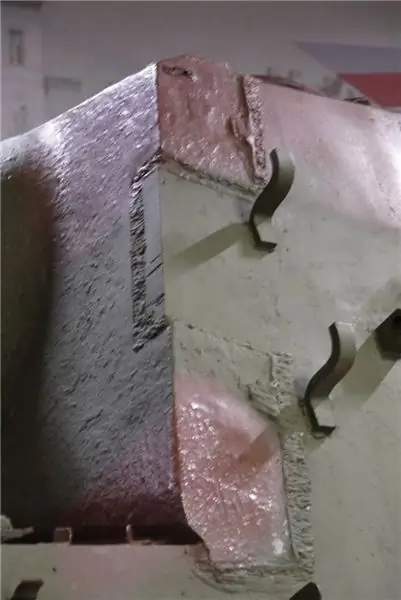
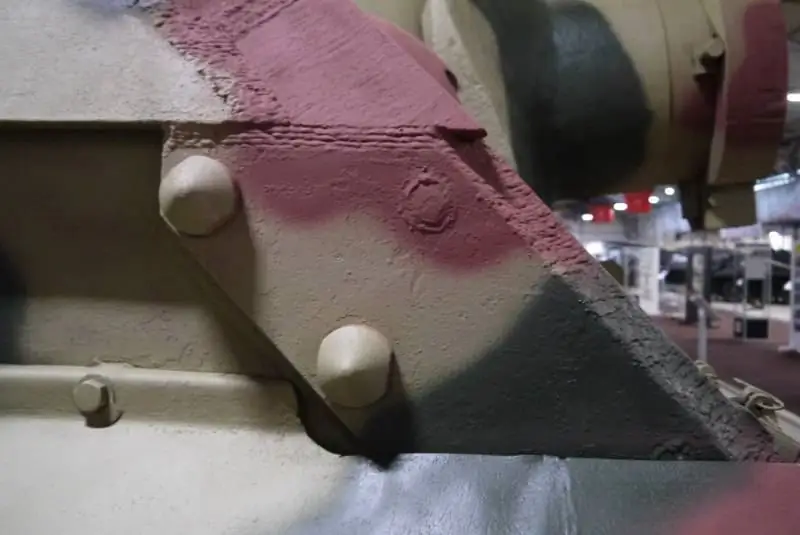
[/مرکز]
همانطور که می دانید ، یکی از ویژگی های متمایز بدنه تانک های آلمانی از سال 1942 اتصال سنبله صفحات زرهی با سنبله مستطیلی یا مایل بود. در همان زمان ، آلمانی ها به یک بیان ساده محدود نشدند - علاوه بر این ، برای استحکام ، کلیدهای استوانه ای یا شاخه ها به مفاصل وارد شدند. به طور خاص ، این در تانک های متوسط "پلنگ" ، اسلحه های خودران "فردیناند" ، برج های "ببرها" سنگین و چند سپاه "ماوس" رایج بود. این شاخه ها رول های فولادی با قطر 80 میلی متر بودند که در اتصالات ورق ها قرار داده می شدند تا پس از مونتاژ برای جوشکاری به آنها متصل شوند. دوشاخه ها در صفحه لبه های سنبله صفحات زره قرار می گیرند - برای هر مفصل یک جفت از آنها لازم بود. در واقع ، پس از نصب کلیدها ، اتصال سنبله حتی قبل از جوشکاری یک پارچه شد. در این حالت ، رولپلاک ها با سطح زره یکنواخت نصب شده و در امتداد محیط پایه جوش داده شده اند. اتصال ناگهانی صفحات زرهی بدنه تانک به طور قابل توجهی حفاظت بالستیکی درزهای جوش و زره را بهبود بخشید. اول از همه ، این امر با افزایش طول کل جوش ، متشکل از قطعات جداگانه ، که انتشار ترک ها را تا حدودی کاهش می دهد ، تضمین شد.
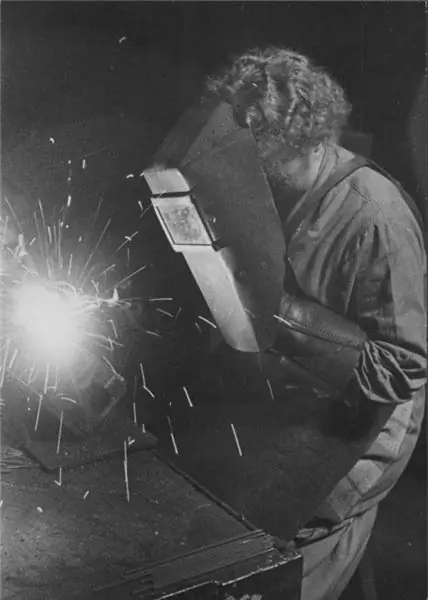
یکی از مشکلات در ساخت بدنه تانک های آلمانی ، ایجاد برش و سوراخ بود (به عنوان مثال ، برای اتصالات زرهی که در بالا ذکر شد). قطع آنها با گاز غیرممکن بود ، بنابراین از حفاری استفاده شد. در ابتدا ، برای فولادهای درجه E-18 و E-19 ، که تحت روش سخت شدن سطح قرار گرفتند ، عموماً یافتن یک مته مناسب غیرممکن بود ، لایه بیرونی زره بسیار سخت بود. در مورد حفر سوراخ قبل از خاموش شدن ، خنک کننده ناهمواری در ناحیه حفره ایجاد شد و به دنبال آن تغییر شکل و ترک شعاعی ایجاد شد. بله ، و در تانک های آلمان شکاف هایی وجود داشت ، و تانک های قابل توجهی ، و تلاش های آلمان برای اجتناب از آنها بعداً مورد بحث قرار خواهد گرفت. تا حدی ، مشکل سخت شدن ناهموار زره در ناحیه سوراخ ها با خمیر نسوز مخصوصی که قبل از ارسال به کوره برای پوشاندن سوراخ ها استفاده می شد ، حل شد. اما ، دوباره ، این تنها بخشی از مشکل را حل کرد. تنها در پایان سال 1944 در موسسه الکتروترمال در اسن بود که این مشکل با یک روش تعدیل محلی در منطقه سخت شده زره حل شد. این واحد که توسط آلمانی ها توسعه یافته است ، در مقاله خود توسط برنده جایزه استالین ، نامزد علوم فنی A. A. Shmykov توضیح داده شده است. این مطالب در نسخه تخصصی "بولتن صنعت تانک" ، که در زمان خود مخفی و برای ما آشنا بود ، در پایان سال 1945 منتشر شد. در سال های پس از جنگ ، صفحات وستنیک غنی از تجزیه و تحلیل دقیق ترفندهای مهندسی مهندسان آلمانی بود ، زیرا تجهیزات کافی به دست آمده بود.
اما بازگشت به آزادی محلی زره که در آن سوراخ ها حفر شده بود. اساس واحد الکترود گرافیتی متصل به محل حفاری بود که از طریق آن جریان الکتریکی 220 آمپر و ولتاژ 380 ولت عبور می کرد. در نتیجه ، زره تا دمای معتدل گرم می شود. بسته به ضخامت زره و قطر سوراخ ، این کار بین 7 تا 15 دقیقه به طول انجامید. پس از انجام مراحل سخت شدن ، سختی زره 2-2.5 بار کاهش یافت. قابل ذکر است که صنعت داخلی (از جمله صنعت مخزن) نیز از حرارت فولاد با گرمایش توسط جریان استفاده می کرد - "دانش" آلمان ها فقط در استفاده از الکترود گرافیتی بود.
آلمانی ها و الکترودها
آلمانی ها همچنین هنگام جوشکاری ورق های زره با سختی بالا با محتوای کربن در محدوده 0.40-0.48 vacation از تعطیلات استفاده کردند. این امر برای متخصصان TsNII-48 (موسسه زرهی) در طول جنگ ، زمانی که مهندسان متالورژی به دنبال دستور العمل هایی برای کاهش ترک خوردن زره T-34 بودند ، شناخته شد. همانطور که معلوم شد ، آلمانی ها صفحات زره را در دمای 500-600 درجه (تعطیلات بالا) رها کردند ، و سپس زره های پیش گرم شده را تا 150-200 درجه در چند گذر جوش دادند. جوشکاران از الکترودهایی با قطر بیش از 5 میلی متر استفاده نکرده اند - با توجه به ضخامت زره تانک های آلمانی ، باورش سخت است. الکترودهایی با قطر 4 میلی متر در جریان 120-140 آمپر ، با قطر 5-6 میلی متر-140-160 آمپر کار می کردند. این فناوری باعث شد که ناحیه جوش بیش از حد گرم نشود. این بدان معنی است که یک منطقه سخت شدن و سفت شدن کوچکتر به دست آمده است. علاوه بر این ، پس از جوشکاری ، درز بسیار آهسته سرد می شود - همه اینها در نهایت به آلمانی ها اجازه می دهد تا کم و بیش با شکاف در محل اتصالات جوش داده شده برخورد کنند. علاوه بر این ، بیشتر از الکترودهای آستنیتی استفاده می شد ، که منجر به شکل پذیری بالای جوش و انتقال طولانی مدت آن به حالت مارتنزیتی شکننده شد. مهندسان TsNII-48 ویژگی های چرخه تکنولوژیکی جوشکاری زره تانک را با دقت مطالعه کردند ، که باعث شد این تکنیک ها با موفقیت به چرخه تولید T-34 منتقل شوند. به طور طبیعی ، هیچ کس در صنعت مخزن نمی تواند چنین برنامه سخت و چند لایه ای از درزهای جوشکاری در سراسر بدنه مخزن را بپردازد ، "دانش" آلمانی فقط در بحرانی ترین درزهای مستعد ترک خوردگی استفاده می شود.
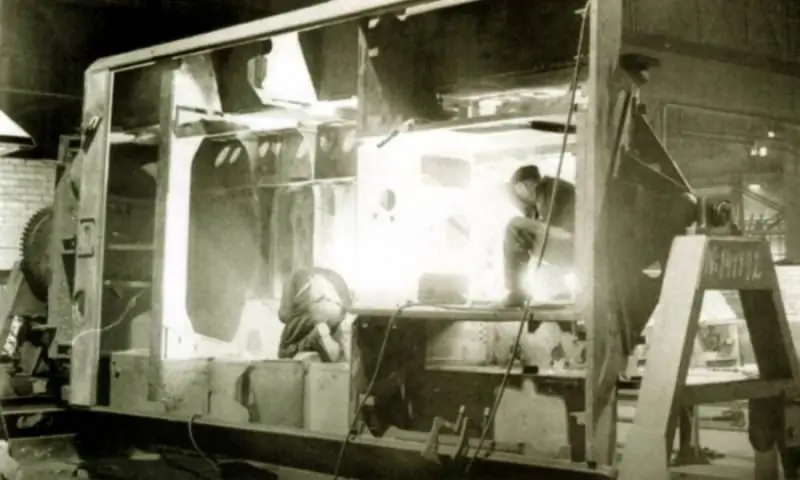
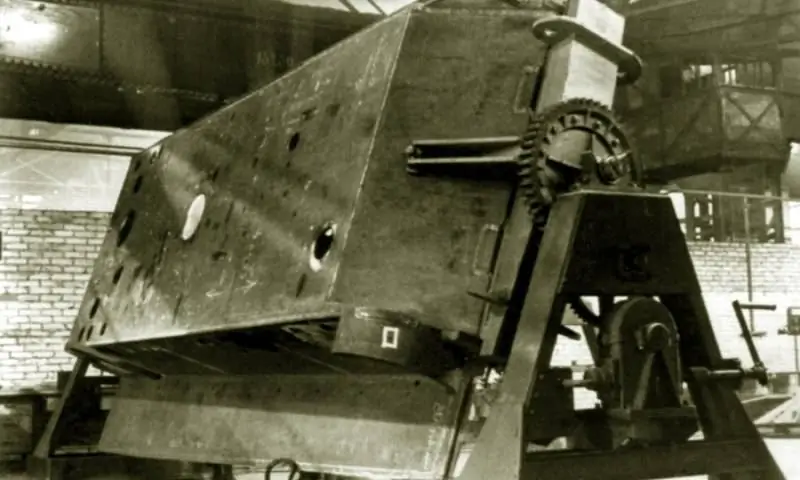
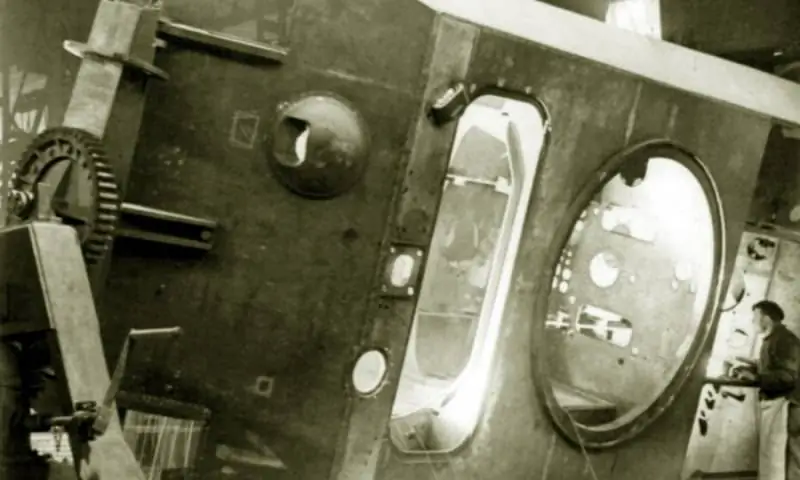
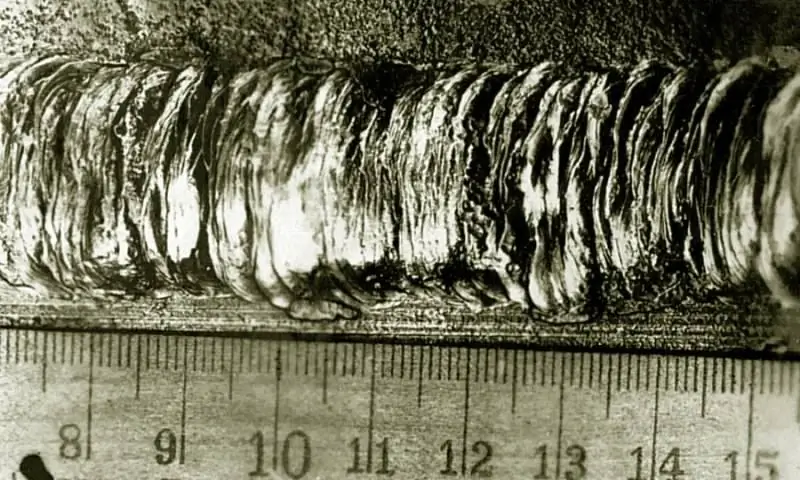
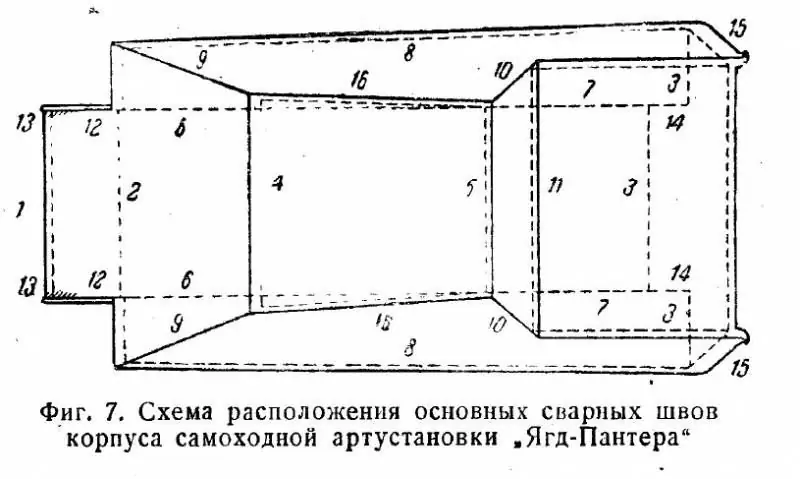
آلمانی ها جوشکاری بدنه مخزن را در شرایط نسبتاً راحت بر روی کج های بزرگ و بدون چسبندگی اولیه انجام دادند (اگرچه در برخی موارد آنها هنوز از یک الکترود 5 میلی متری در تمام طول مفصل عبور کردند).تیلتر سازه ای بود که مانند یک تف ، لاشه یک تانک آلمانی حول محور طولی می چرخید. درایو دستی یا برقی بود. با توجه به دقت برش بالا ، شکاف بین قسمتهای بدن مونتاژ شده بر روی روتاتور (حداقل در دوره اصلی جنگ) 3-4 میلی متر نیست. در غیر این صورت ، از واشرهای فولادی استفاده شد. درزهای بلند توسط جوشکارها به چند حلقه کوچک شکسته شده و همزمان در یک جهت جوش داده شده است. درزهای بسته نیز توسط دو جوشکار همزمان به یکدیگر جوش داده شد. این حداقل تنش سخت شدن فولاد و یکنواخت ترین توزیع را تضمین می کند. با توجه به یکی از افسانه ها ، که توسط الکساندر ولگین در ماده "قاب برای جنب و جوش آلمانی" بیان شد ، حقوق جوشکاران در برخی از شرکت های رایش سوم قطعه کار بود - برای جرم فلز ذخیره شده در مخزن.
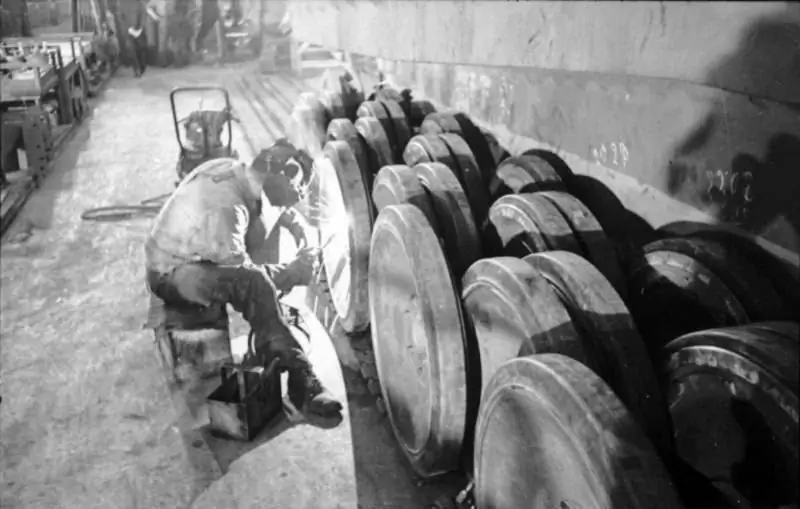
نیازی به صحبت در مورد قوانین خاصی برای کنترل درزهای جوشکاری در صنعت مخازن آلمان نیست - هیچ اشعه ایکس ، تشخیص نقص مغناطیسی ، و هیچ حفاری اولیه وجود نداشت. و ترک هایی در درزها وجود داشت! اگر طول آنها تا 100 میلی متر باشد ، آنها را آسیاب کرده و جوش داده اند ، و اگر بیشتر ، آنها را با قوس الکتریکی ذوب کرده و نیز جوش داده اند. آنها همچنین با ترک های تشخیص داده شده در زره اصلی نیز همین کار را کردند. به هر حال ، با گذشت زمان ، آلمانی ها به دلیل ترکیبات جدید الکترودها موفق شدند نسبت ترک ها در درزهای جوش داده شده را از 30-40 to به 10-20 reduce کاهش دهند. همچنین از روشهای متناوب عبور در جوشهای چند لایه با الکترودهای آستنیتی و فریت استفاده شد.